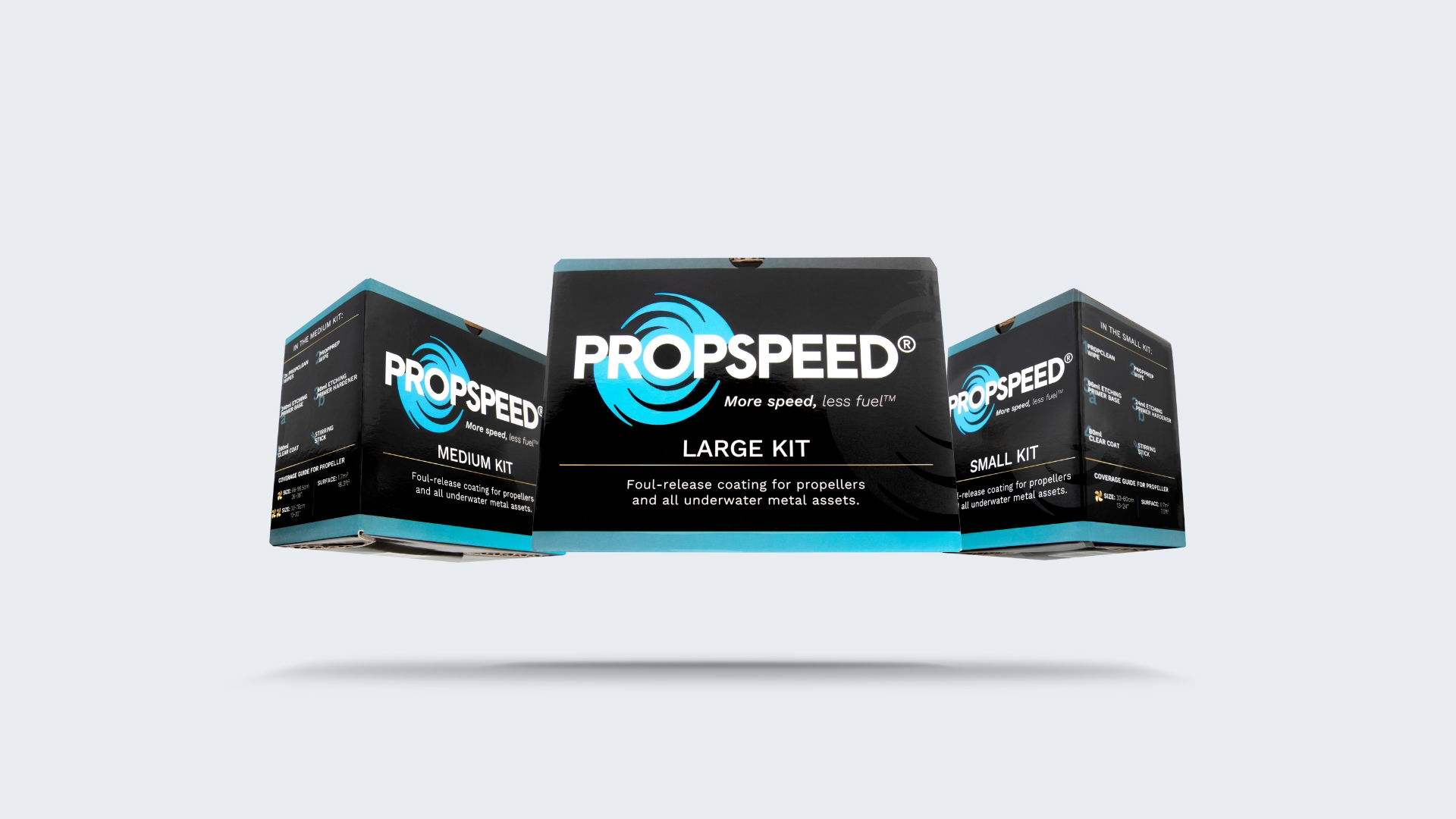
Summary
Corrosion; a boat owner’s greatest fear yet also one of the most misunderstood. The five most prevalent forms; galvanic, stray current, oxidative, environmental, and crevice corrosion should be understood in order to take the correct steps to either prevent or successfully remedy an identified problem.
About
Galvanic
All metals have an electrical potential when submerged in salt water (electrolyte). Galvanic corrosion occurs when two dissimilar metals are connected, either physically or through an electrical connection within the same electrolyte. Called a galvanic cell, the more active (anode) metal will sacrifice itself to protect the more noble metal (cathode). For example, a bronze propeller on a stainless steel shaft will sacrifice to protect the shaft. Protecting from this form of corrosion is essentially the job of anodes. By introducing a more active or “anodic” metal to the galvanic cell – you thereby determine the sacrificial anode.
Stray Current/Electrolytic
Electrolytic, or stray current corrosion, is corrosion activity induced by the presence of stray electrical current. The source and type of electric current will usually determine the type of damage found. Typically DC power is the culprit for aggressive corrosion causing rapid anode dissipation and/or devastating corrosion effects in usually short periods of time. Common culprits are insulation failure of wiring or appliances, earth leakage from devices such as bilge pumps and alternators or externally through common shore power connection where galvanic isolation is not installed or operating correctly. Good maintenance and high electrical fitness are necessary to prevent this action. However not always foreseeable, expert assistance should be sought to correctly diagnose and rectify this problem from quickly becoming an expensive and heartbreaking episode.
Oxidative
Oxidative corrosion, otherwise known as surface corrosion, occurs when a bare metallic surface reacts with oxygen, causing a local reaction and corrosion of the surface. Galvanic and stray current corrosion can also worsen this reaction, and metals such as bronze and aluminium are particularly vulnerable. The best protection against oxidative corrosion is through the use of coatings, isolating the substrate from oxygen, therefore preventing a reaction.
Crevice
Crevice corrosion is a very specific form of corrosion that corrodes stainless steel in particular. Stainless steel doesn’t corrode like regular metal due to the formation of a tightly adhering layer of chromus oxide on the surface of the metal, protecting the metal from corrosion. However, this coating can only form in the presence of oxygen. Small crevices that do not allow exposure to oxygen, but allow for moisture to enter result in the break down of the protective coating and allow for stainless steel to corrode. This is commonly seen between pipe threads, stern tubes and under bolt heads.
Environmental
Corrosion can also be aggravated and/or caused by multiple environmental factors, such as water temperature, humidity, exposure to oxygen and salinity. Understanding these different factors and how they may be contributing to your corrosion problem will help you to take the appropriate measures to protect against corrosion.
So how can you minimize corrosion? The main methods include anodes, coatings, good maintenance and shore power isolation (galvanic isolator). Firstly, the use of sacrificial anodes will control the risk of galvanic corrosion. Understanding what metals you are protecting will give rise to the correct anode to use. The incorrect anode can either result in under-protection (galvanic corrosion) or over-protection, which will result in poor coating performance and potentially coating failure (a process called cathodic disbondment). Marine Protection Systems (www.marineprosystems.com) is one business that understand the importance of anode selection to ensure the best efficiencies and performance.
The use of a paint or coating to protect the metal, by essentially isolating the metal from oxygen and the electrolyte. Quality underwater metallic coatings, like Propspeed reduces the risk of corrosion by electrically isolating the metal, as well as limiting the exchanges between the ions and the gases contained in the water and the metal. In short, if a reaction can’t occur, there will be no corrosion! Combining a great coating with the right anode will ensure efficient cathodic protection and the best coating performance and longevity.
Explore our key strategic partnerships, expert articles, endorsements from industry-leading OEMs and more.